Diesel exhaust systems face extreme heat, soot, and chemicals. Proper maintenance—from turbo to tailpipe—helps avoid costly breakdowns and emissions penalties.
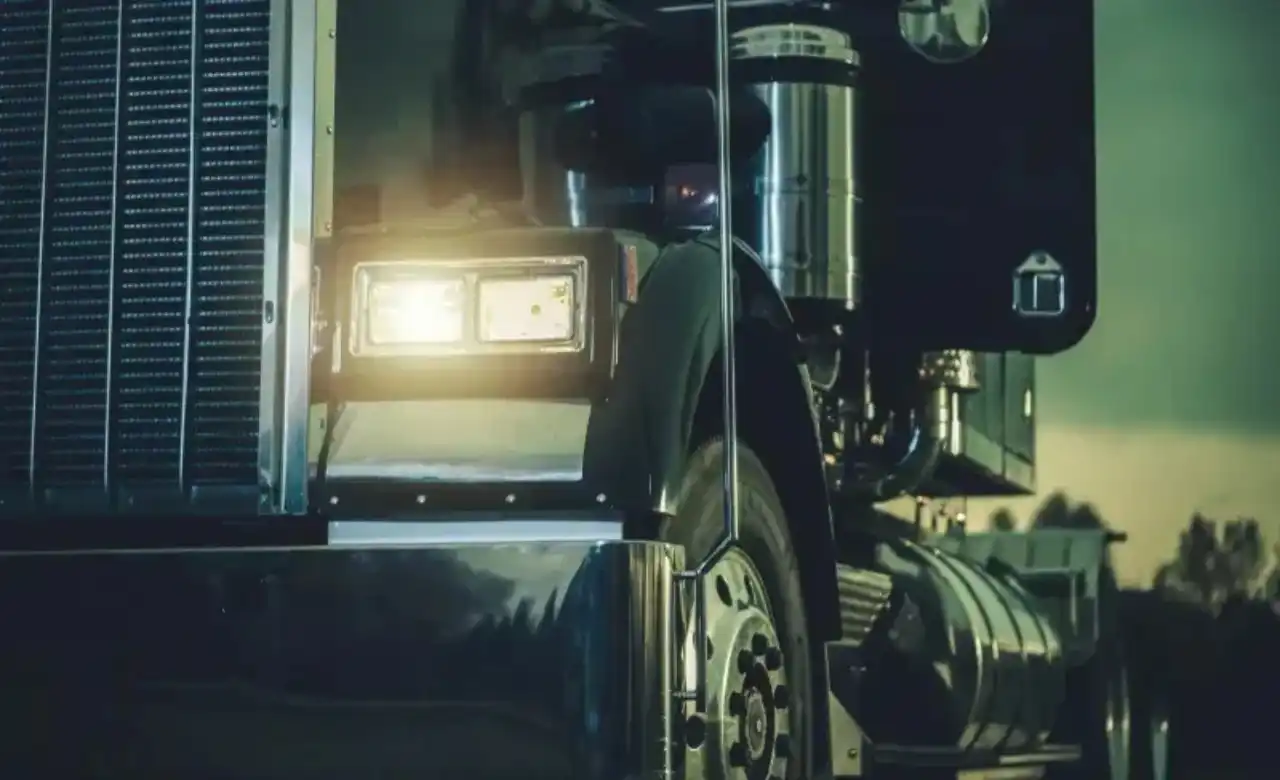
In the world of heavy-duty diesel trucking, every component has a purpose, but few endure as much punishment as the exhaust system. From handling searing temperatures to filtering out particulate matter and chemicals, this system plays a crucial role in keeping your engine compliant, efficient, and operating safely.
For fleet operators in places like Irving, TX, where emissions regulations are increasingly stringent and fleet uptime is non-negotiable, understanding the life cycle of the heavy-duty exhaust system isn’t just useful—it’s essential.
The Journey Begins: Exhaust Gases Post-Combustion
When diesel fuel ignites within the engine’s combustion chamber, it generates explosive power, and along with it, a stream of superheated exhaust gases. These gases must be efficiently routed away from the engine to maintain optimal performance and safety. Exhaust gases are made up of several byproducts, including:
- Nitrogen oxides (NOx)
- Particulate matter (soot)
- Carbon monoxide (CO)
- Hydrocarbons (HC)
Left unchecked, these gases would wreak havoc on the environment and your equipment. Fortunately, modern diesel trucks are outfitted with after-treatment systems that mitigate these risks.
Core Components of a Heavy-Duty Exhaust System
Understanding each component in the exhaust system reveals not only how the system functions but also how and why it fails over time.
Turbocharger
As the gases exit the engine, they first pass through the turbocharger. This unit harnesses the force of the exhaust stream to compress and push more air into the combustion chamber, improving power and fuel efficiency.
However, the turbo endures extreme thermal and mechanical stress. When the oil supply is insufficient or dirty, bearings wear prematurely. Excessive soot can coat turbine blades, reducing efficiency and eventually leading to failure.
Diesel Oxidation Catalyst (DOC)
Next in line is the DOC, which serves to reduce carbon monoxide and unburned hydrocarbons by oxidizing them into less harmful substances, such as carbon dioxide and water vapour. It also helps raise exhaust temperatures—a critical requirement for DPF regeneration.
Because the DOC is a catalytic converter, it relies on precious metals to trigger oxidation. These catalysts can become coated with soot or oil if upstream issues arise, which can diminish performance and necessitate replacement.
Diesel Particulate Filter (DPF)
The DPF is where things get dirty. This ceramic filter traps and stores soot, keeping it from entering the atmosphere. However, it’s a finite container—it must periodically clean itself through regeneration, a process that uses high heat to burn off accumulated carbon. There are three types of regeneration:
- Passive (natural during driving conditions)
- Active (initiated by the engine)
- Forced (manual intervention required)
Frequent forced regens are a red flag, indicating deeper issues such as failed sensors, fuel injector problems, or incomplete combustion.
Selective Catalytic Reduction (SCR)
To tackle NOx emissions, exhaust gases enter the SCR catalyst, where Diesel Exhaust Fluid (DEF) is injected. DEF is a urea-based solution that reacts with NOx gases, converting them into nitrogen and water vapour.
The SCR system is both effective and fragile. Issues such as contaminated DEF, clogged injectors, or faulty NOx sensors can result in reduced performance, increased emissions, and failed inspections.
Tailpipe and Sensors
Finally, after passing through all filtration and treatment stages, the cleaned exhaust exits through the tailpipe. Along the way, various sensors monitor temperature, pressure, and the content of emissions. If any reading falls outside of acceptable ranges, it can trigger a check engine light and initiate a derate condition, limiting engine power.
Enemies of the Exhaust System
The exhaust system operates in an unforgiving environment. Understanding its primary adversaries—heat, soot, and chemicals—can help identify failure risks and prevention strategies.
Heat
Exhaust temperatures can reach over 1,200°F under heavy load. This heat expands and contracts metal components repeatedly, leading to:
- Cracked manifolds
- Warped flanges
- Leaking gaskets
- Melted sensor wires
Prolonged exposure without proper maintenance leads to component failure, compromised efficiency, and emissions violations.
Soot
Soot is produced when combustion is incomplete—something that can occur more frequently due to the use of low-quality fuel, excessive idling, or malfunctioning injectors. This carbon residue clogs filters and coats sensitive components, such as sensors and catalysts. Left unchecked, it causes:
- DPF overload
- Frequent regen cycles
- Sensor misreads
- Performance loss
Chemicals
The exhaust stream is a chemical minefield, complete with acids, residues, and reactive gases. Add to that the external environment: road salt, moisture, and DEF crystallization, and it’s easy to see why corrosion is such a prevalent issue.
Even stainless steel pipes and brackets will eventually succumb if preventive measures aren’t taken, especially in humid or high-salt areas.
The Maintenance Lifecycle
To ensure longevity and prevent costly breakdowns, heavy-duty exhaust systems must be inspected and maintained routinely. Here’s how to keep yours in top condition.
Routine Visual Inspections
Visually inspect the entire exhaust route, from turbo outlet to tailpipe. Check for:
- Cracks or leaks in exhaust pipes
- Missing or loose brackets and clamps
- Corrosion on hangers or sensors
- White crusting (sign of DEF leaks)
Addressing minor issues early prevents them from becoming major failures down the road.
Sensor Health Checks
Modern trucks depend heavily on accurate data. NOx, DPF pressure, and temperature sensors are critical to mission success. Faulty readings will trigger fault codes, incorrect regens, or derates. Use diagnostic tools to verify sensor output, especially after a repair or during preventive maintenance (PM) intervals.
Scheduled DPF Cleaning
DPF filters don’t last forever. Even with regular regeneration, ash (a byproduct of engine oil additives) builds up and eventually clogs the filter. This requires professional cleaning or replacement.
Industry guidelines recommend DPF cleaning every 200,000–250,000 miles, or more often for vocational fleets operating in stop-and-go environments.
DEF System Maintenance
Store DEF in sealed containers and monitor expiration dates. Crystallized DEF wreaks havoc in injection lines and SCR components. Regularly flush and inspect DEF tanks and delivery lines for contamination.
Low-quality or off-spec DEF not only damages your system, it also voids most OEM warranties.
When Problems Arise
The warning signs of a failing exhaust or after-treatment system are initially subtle. But over time, minor symptoms snowball into significant issues. Common symptoms include: